1. Why did statistical quality control ideas catch on in the
1940s?
2. Suppose you make electronic calculators that contain a
chip purchased from a local vendor. How would you
decide how much inspection to perform on the chips
supplied to you?
3. For the following situations, comment on whether inspec–
tion by variables or by attributes might be more appropriate:
a. Filling packaged food containers to the proper weight.
b. Inspecting for defects in cloth.
c. Inspecting appliances for surface imperfections.
d. Determining the sugar content of candy bars.
4. Workers should be given more control over the inspec–
tion of their own work. Discuss the pros and cons of
this proposition.
5. Why are most processes not in statistical control when
they are first sampled for control chart purposes?
6. Define the purpose of continuous improvement of quality.
7. How is a Pareto chart used to improve quality?
8. Which technique would be useful for each of the
following situations?
a. To rank-order the causes of a quality problem.
b. To brainstorm the reasons why a product might have
failed.
c. To find an assignable cause.
d. To determine if a process range is under control.
e. To reduce the variability of failures found in the
field under actual use of the product.
f. To achieve the smallest possible variance in the time
it takes to wait on tables in a restaurant.
9. A cause-and-effect diagram is used to identify the pos–
sible causes of defects. Draw a CE diagram for the fol–
lowing situations:
a. Your car doesn’t start in the morning.
b. You received a low grade on your last exam.
c. A student fails to graduate from college.
10. It has been said that Six Sigma is a metric, a process for
improvement, and a philosophy for managing a busi–
ness. Explain these different perspectives.
11. Use the DMAIC steps to describe and improve the pro–
cess of ordering a book from an Internet retailer. From
the perspective of the retailer, what would be done in
each of the steps?
12. How can lean and Six Sigma approaches work together
in making process improvements?
13. If an organization was using neither lean nor Six
Sigma, how would you decide which approach to
use first?
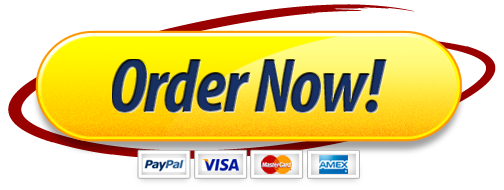