1. Identify the different types of inventories (raw materials, work in process, and finished goods) carried in the following organizations: gas station, hamburger stand,
clothing store, and machine shop. What functions (purposes) do these inventories perform?
2. Why are stockout costs difficult to determine? Suggest an approach that might be used to estimate them.
3. What is the difference between a requirements philosophy and a replenishment philosophy of inventory man agement? Why is this difference important?
4. Compare and contrast the management of finished goods inventory in a manufacturing firm with that in a retail or wholesale firm.
5. For a given service level, why does a P system require a larger inventory investment than a Q system? What factors affect the magnitude of the difference?
6. Suppose you are managing the Speedy Hardware Store. Give examples of items that might be managed by a P system and other items for which a Q system might be
used. How do these items differ?
7. How should a manager decide the appropriate service level for finished goods items? Should some items have a 100 percent service level?
8. What is the appropriate role of inventory turnover as a measure for evaluating the management of inventory? Under what circumstances is high turnover detrimental
to a firm?
9. Suppose you are managing a chain of retail department stores. As a top manager, how would you measure the overall inventory management performance of each
store? How would you use this information in your rela– tionship with the individual store managers?
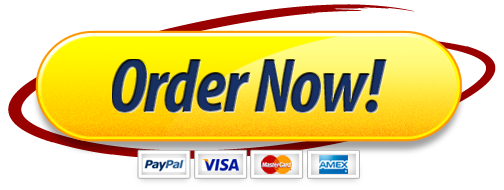